
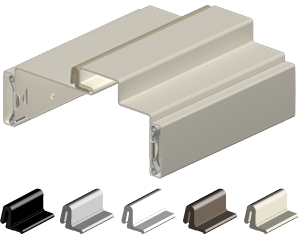
Dassault Systèmes’ software solutions support BMW in core areas for design and manufacturing process planning, with CATIA as the backbone for product development.Īutodesk is another technology supplier in this area, delivering software particularly targeted at new assembly line commissioning, having recently launched its Autodesk Factory Design Suite, a new 2D and 3D solution that simplifies layout of manufacturing facilities and production machine lines. Additionally, Tesla is using the CATIA ICEM solution for Class-A surfacing and DELMIA Human for occupant ergonomics.ĭassault Systèmes has also signed a five-year global agreement with BMW that will not only improve its automotive product offering but also the BMW development and production process. With two phases already implemented, future phases will migrate Tesla’s product authoring solution from CATIA V5 to CATIA V6. DELMIA was used to define an optimised assembly sequence, which was shared with other departments, including production associates, whose input was valuable in developing a final design optimised for both function and production.Īnother recent convert to Dassault Systèmes latest PLM solutions (V6) is electric car manufacturer Tesla Motors, based in Palo Alto, California. With regards to doors, 204 parts must be efficiently assembled into each aluminium-skinned door assembly. The methodology at Bentley is a good example of PLM in action, where digital technology exploitation now encompasses a complete virtual build. The same data is presented in DELMIA, where manufacturing associates can plan and simulate manufacturing processes in parallel with design evolution.” “All data is managed in ENOVIA and all departments access this data concurrently. “The foundation stone for being able to exploit these technologies revolves around our ability to manage all of our information in a single database,” he continues. Aftersales and service teams, for example, now have concurrent access to our evolving 3D data, allowing teams to construct technical illustrations in parallel with the design evolution process using 3DVIA Composer. We are now able to integrate wider business departments in our quest to exploit digital data. John Unsworth CAD Strategy Manager at Bentley adds: “3D provides greater stakeholder cognition, allowing extended input to design and production scenarios at a timely point. This methodology, facilitated with Dassault Systèmes DELMIA, included 3D reviews at regular ‘virtual build’ meetings where 3D visualisation allowed production build associates to make valuable contributions to the design process and influence the design based on their experience and specialist knowledge. “Using this data, a detailed assessment of the build process was carried out and any potential build concerns were identified and resolved much earlier in the design process.” “We used Dassault Systèmes’ manufacturing simulation tools to model 831 build operations across 30 stations – the complete build process was simulated in 3D,” he says.
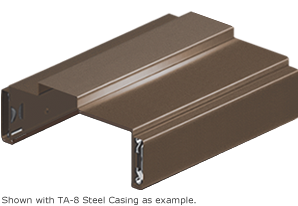
Ian Swann, Senior Virtual Assurance Engineer at Bentley describes how 3D technology was used to develop the new model. It takes nine weeks to build a Mulsanne, over which time around 10,500 parts are brought together and assembled. At the company’s plant in Crewe, UK, the luxury carmaker is using Dassault Systèmes’ PLM solutions, including CATIA, ENOVIA, DELMIA and 3DVIA, to exploit 3D visualisation and simulation techniques across core product lifecycle processes for the recently-launched Mulsanne. AMS Automotive Evolution Summit On-Demand.
